电动汽车热泵系统超疏水换热器抑制结霜性能研究
导读
Reading guide
针对电动汽车冬季制热能耗高,影响续航里程的问题,研究了表面浸润性对电动汽车热泵系统换热器结霜性能的影响。通过对超疏水表面冷凝、结霜过程的微尺度定量表征,发现超疏水表面液体合并自弹跳现象是抑制结霜的重要因素,为了在全尺寸换热器上实现抑制结霜效果,利用水热法及低表面能处理方法对换热器进行了超疏水处理,并进行了制热工况结霜试验,结果显示,与未作处理的原始换热器相比,超疏水换热器结霜时间延长70%以上,单位时间内化霜次数减少40%以上。
关键词:超疏水换热器 ;抑制结霜 ;液滴合并自弹跳
作者:孔祥潼1,2刘涛3王树义4李龙男1李炜1
1、中国科学院长春光学精密机械与物理研究所,微纳光子学与材料国际实验室 发光学及应用国家重点实验室,长春 ;
2、中国科学院大学,北京 ;
3、中国第一汽车股份有限公司研发总院,长春 ;
4、富奥汽车零部件股份有限公司热系统事业部,长春
传统的内燃机汽车以发动机的余热作为热源向乘员舱供暖,而电动汽车需要消耗动力电池的能量来维持乘员舱内部的温度。目前,电动汽车普遍采用正温度系数(Positive Temperature Coefficient,PTC)热敏电阻的电加热方式向乘员舱提供热量。PTC 热敏电阻虽然具有适应低温环境、成本低、系统简单、易于在电动汽车上集成等优点,然而其能效比(Coefficient Of Performance,COP)最大值不超过1 [1]。因此,在以我国东北地区为代表的高纬度地区,PTC热敏电阻的高耗能特性严重限制了电动汽车在冬季的续航里程[2-3]。
相比于PTC热敏电阻的制热模式,车载热泵系统具有更高的COP.是一种更高效、节能的冬季制热方式车载热泵系统根据不同工作温度使用不同的冷媒工质如四氟乙烷(C,H,F,R134a)和二氧化碳(CO.)等。车载空气源热泵系统在冬季制热模式工况下,室外换热器作为蒸发器.通过换热器微通道内部冷媒工质的蒸发过程吸收外界环境的热量,车内冷凝器通过冷媒工质的冷凝过程向车内释放热量实现供暖。然而,由于系统中冷媒工质的相变温度通常低于0°C,当室外蒸发器扁管及翅片表面温度降至水的冰点温度时,引起蒸发器表面结霜,进而增大换热器表面热阻、提高换热器的压降57,极大地减弱换热器的换热效率。为了维持热泵系统的换热性能,需要通过热泵系统的逆循环、热气旁通或电加热等方式进行除霜”消耗动力电池的电能,影响电动汽车的续航里程。为了解决上述问题,近年来,以超疏水表面为代表的被动式抑霜技术受到了广泛关注,并被视为一种有效降低空气源热泵系统除霜能耗的方法。本文通过研究铝基超疏水表面在低温条件下抑制冷凝与结霜的微观过程.验证超疏水表面应用于车载热泵系统空气源换热器抑制结霜的可行性,通过开发大型电动汽车换热器表面超疏水处理工艺制备超疏水换热器样品,分析超疏水换热器的抑制结霜机理,并对制热模式下的换热器结霜性能进行测试.以期为新型纯电动汽车热泵型空调系统的换热器被动式抑制结霜提供全新的解决思路。
01
实验方法
在微观冷凝/结霜试验中,以光滑铝合金作为基底材料,对样品表面分别进行了“未处理”“疏水处理”以及“超疏水处理”,以研究不同表面浸润性对冷凝和结霜过程的影响。未处理样品的主要制备过程是将铝合金品(2.5cmx25cm)放入乙醇中超声清洗5min.清除表面杂质,清洗后取出吹干。疏水处理样品的制备过程是将经过上述清洗吹干后的铝合金样品放入密闭腔室内进行低表面能改性处理,具体是在85C加热条件下,利用化学气相沉积方法将全氟癸基三乙氧基硅烷
(Heptadecafluorodecyl- TriMethoxy- Silane,HTMS)沉 积到铝合金样品表面上,沉积3h。超疏水处理样品的制备过程是将清洗后的铝合金样品放入90 ℃去离子水中加热 10 min,水热处理后取出吹干,然后放入密闭腔室内进行低表面能处理[14]。制备后的样品分别利用扫描电子显微镜观察表面微观形貌,并通过表面静态接触角来表征表面的浸润性。如图1所示,未处理的样品表面光滑平整,只有原始的抛光打磨纹路,其接触角(Contact Angle,CA)约为60°,表现出亲水性。经过低表面能处理的疏水处理样品表现出一定的疏水性,接触角增加到104°。而超疏水处理样品由于经过水热处理,表面生长出百纳米尺度的片状纳米结构(见图1b),能有效增加表面粗糙度,结合低表面能处理后接触角达到165°
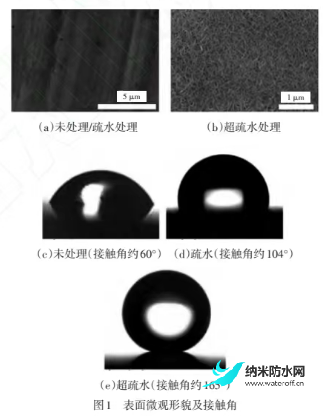
试验装置/平台
为表征不同浸润性表面的冷凝/结霜微观过程,搭建了微观尺度表征平台,样品采用导热硅脂固定在温度可控制的冷台(PE-120,Linkam)上以减少传热热阻。冷凝/结霜过程主要通过配备高倍物镜(TUPlanFluorEPI,20×,Nikon)和相机(DS-Qi2,Nikon)的显微镜平台进行观察和记录。液滴合并自弹跳过程由高速相机(Phantomv711,VisionResearch)记录,并用传感器(HX93BDV0,Omega)对试验过程中的环境温度及湿度进行实时测量。
02
超疏水表面液滴合并自弹跳现象
在微观尺度下表征超疏水表面液滴合并自弹跳过程中,使用压电分配器在超疏水表面放置2个半径约为260μm的大小相等的液滴,使它们能够聚在一起,并用高速摄像机从侧面观察合并自弹跳过程,如图2所示。当2个液滴触碰到一起时发生合并,由于水热法处理后的铝合金表面形成了均匀致密的片状纳米结构,使液滴表面粘附力降低,在Cassie-Baxter润湿状态下通过2个微液滴之间形成的液桥与超疏水表面的相互作用,将表面能转化为合并液滴的动能,最终实现了液滴合并自弹跳,脱离表面[15]。

冷凝及结霜过程微观表征
如图3所示,不同浸润性表面的冷凝过程表现出不同的特征。在试验条件为冷台温度-15℃,环境温度20℃,湿度60%的情况下,表面上不断有液滴形成和长大。未经处理的样品表面具有较小的接触角,水汽逐渐在表面上冷凝形成微小不规则形状的液滴,这些液滴会逐渐合并并最终形成较大的形状不规则的大液膜。相比之下,经过疏水处理的样品表面具有一定的疏水性和较大的接触角,在冷凝过程中,液滴的分布较为独立,且液滴边缘形状多为较规整的圆形。而经过超疏水处理的样品表面,多数形成边缘规整的球形液滴。在相同时间下,可以明显观察到超疏水表面上的液滴覆盖面积更少。在图3c中,表面上2个相邻的液滴合并后离开表面,实现表面液滴的合并自弹跳(自排离),减少液滴在表面的覆盖面积,而未处理及疏水处理的样品表面上,2个相邻液滴合并后形成更大的液滴仍留在表面上,最终增加形成结霜层的可能性,并增加换热器表面的热阻(见图3a、图3b)。
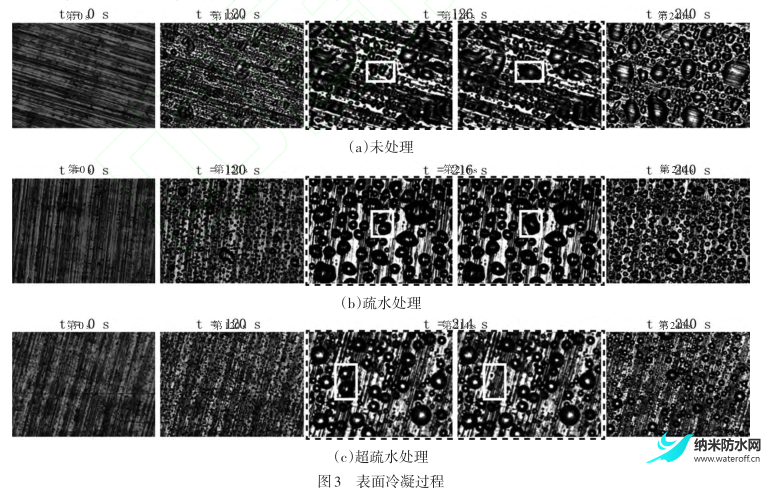
图4展示了样品表面的结霜过程。当视野内四周的液滴开始出现少量冻结时,未处理表面上视野内的液滴在8s内完全冻结。疏水处理表面上的液滴在45s内完全冻结。而超疏水处理表面上的液滴完全冻结的时间约为240s,同时可以看到,表面仍有大部分区域未结霜。通过多次试验测量,统计了3种不同表面的结霜速度性能,结果如图5所示,超疏水表面的结霜速度最缓慢,约为0.003mm2/s。
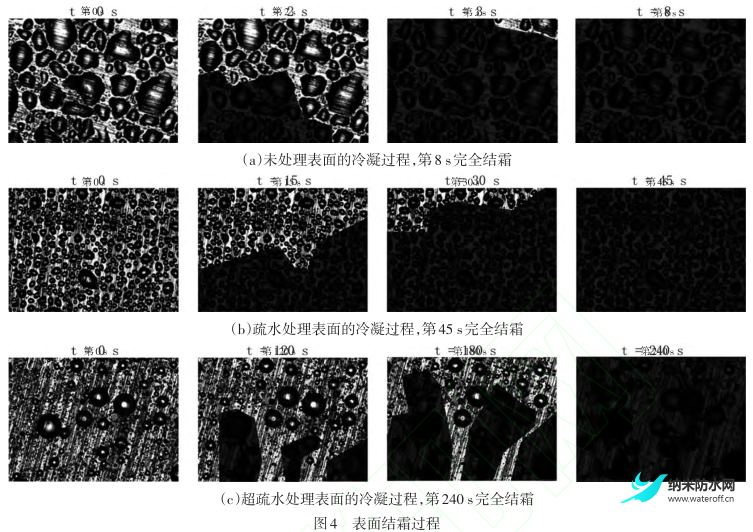
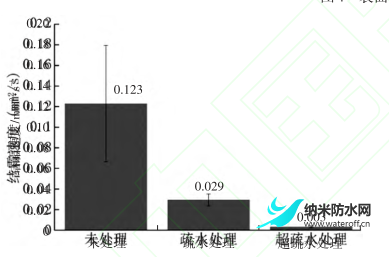
超疏水表面抑制霜层形成的主要原因有:
a.相比于其他表面,超疏水表面的表面能更低,液滴冷凝成核密度也相应更小。同时,因为在超疏水表面上存在液滴自弹跳现象,2个未冻结的液滴长大触碰时,会合并形成更大的液滴并弹跳离开表面,减少了超疏水表面液滴的覆盖面积,从而有效减少了霜层在超疏水表面的覆盖面积[14,16-17]。
b.相比未经处理的表面,超疏水表面具有更大的接触角,形成球状液滴,液滴底部与冷表面的接触面积更小,因此更少的热量从液滴传递到表面,从而使得超疏水表面上的液滴冷冻速度更为缓慢[17-18]。
c.考虑大面积的结霜过程,其表面结霜过程由边缘区域的冷点优先冷冻液滴,再向中间的液滴扩散。液滴间的结霜过程由霜晶枝生长,并接触到附近液滴形成冷桥,发生冷冻转移。由于超疏水表面液滴具有更大的接触角,相比未经处理的表面,相同体积的液滴在表面上的投影面积更小,液滴间的冷桥形成更为缓慢。同时,由于超疏水表面液滴在冷凝过程中会合并自弹跳,减少液滴的覆盖面积,在结霜过程中,可以有效抑制冷桥形成及霜层的扩散[10-11,19]。
超疏水换热器的制备及结霜测试
超疏水表面上的冷凝及结霜微观表征结果说明优化设计的表面纳米结构和低表面能改性方法可以使超疏水表面具有抑制结霜、强化换热的特性。为了把该设想与微尺度试验结果在全尺寸车载热泵换热器上进行验证,本文开发了一种大型换热器超疏水处理工艺。如图6a所示,试验中采用某型号全尺寸车载微通道换热器(尺寸为70cm×50cm×5cm)作为测试样品,其具体表面超疏水处理所使用设备及制备流程如图6b和图6c所示,其制备过程中所使用的方法与上述超疏水样品的制备流程相近。
为了研究超疏水表面处理方法对换热器结霜性能的影响,利用标准风洞测试平台对制热模式工况下的换热器抑制结霜性能进行了研究。试验工况如图7所示,在约1500s后,风洞系统以及换热器内部制冷冷媒的运行工况保持相对稳定,并在试验过程中保持75%±5%的相对湿度以及2℃的干球温度。在启动制冷剂循环后,换热器表面逐渐开始有液滴冷凝生成,并在换热器表面温度进一步降低的过程中产生结霜,导致压降增大。如图8所示,在2500s的测试后,未处理换热器表面和超疏水换热器表面的结霜覆盖面积展示出明显的区别,超疏水换热器表面上的霜层覆盖面积更小,该结果说明超疏水换热器与未处理的换热器相比具有更好的抑制结霜性能。
为了定量比较未处理换热器与超疏水换热器的抑制结霜性能.图9a给出了2个换热器结霜过程中压降随时间变化的关系。从工况稳定后开始计算:当压降由45Pa提高至55Pa时,2种换热器所需的时间分别为230s和390s,与未处理换热器相比,超疏水换热器的结霜时间延长了160s,约为70%;当压降由45Pa提高至62Pa时,2种换热器所需的时间分别为470s和1190s,与未处理换热器相比,超疏水换热器的结霜时间延长了720s,约为153%。该结果表明,车载热泵系统在制热工况下运行时,超疏水换热器具有优异的延迟结霜效果。在不同的环境温度、湿度工况下,超疏水换热器表面的冷凝和结霜过程会受到影响,超疏水换热器的延缓结霜特性也会随工况相应改变,相比于未处理的换热器,超疏水换热器仍具有较好的抑制结霜性能[11]。图9b对比了2种换热器在单位时间内(1h)所需的化霜次数。当压降由45Pa提高至55Pa时进行化霜,相比于未处理换热器,超疏水换热器所需化霜次数减少约40%;当压降由45Pa提高至62Pa时进行化霜,相比于未处理换热器,超疏水换热器所需化霜次数减少约57%。
超疏水换热器含水率试验
为了研究超疏水处理对换热器冷凝水排出性能的影响,利用天平对换热器进行含水率测试。试验装置如图10所示,将换热器插入水槽中浸泡1min后取出,测量初始含水率,然后将换热器挂起,测量换热器的排水性能,图11比较了2种换热器含水率在15min排水试验过程中的变化情况。在浸泡1min后,超疏水换热器表面大部分未被浸润,残留的水分较少,超疏水换热器的含水率约为9.4%。而未处理的换热器表面表现为亲水状态,在浸泡过程中完全被浸润,取出后残留有大量的水分,含水率约为58.7%。在15min内,水在重力作用下排出,未处理的换热器含水率在最初的1min内快速下降,随后缓慢下降至30.2%,而超疏水换热器因本身具有超疏水特性,表现出较低的含水率,在15min排水试验过程中含水率变化不大,但含水率依然较未处理的换热器低。试验结果表明,在车载热泵系统制热模式中,超疏水换热器在化霜条件下可以快速排出融霜,保持换热器翅片的高效换热性能。
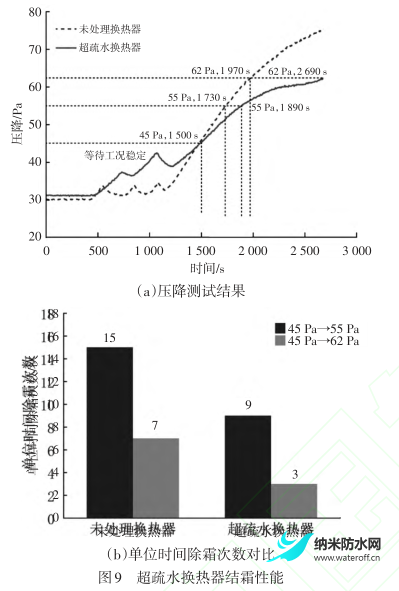
超疏水换热器耐久性及使用寿命
根据经典Cassie-Baxter模型对表面超疏水性能的描述,超疏水表面的浸润性由表面的粗糙度和表面吉布斯自由能共同决定,超疏水换热器主要采用水热法制备表面纳米结构,并利用硅烷(HTMS)对纳米结构表面的浸润性进行改性,降低其表面能,获得了铝基超疏水纳米结构表面。在实际应用中,通过表面处理获得超疏水性能的方法形成的表面微纳结构和化学组分会受到外部环境的影响,出现被破坏的现象,进而影响表面浸润性和超疏水表面器件在应用中的寿命。为此,对超疏水换热器表面微纳结构和化学组分的使用寿命进行分析。
首先,在超疏水换热器表面上形成的纳米结构,是通过水热法在翅片铝基表面形成的致密的纳米尺度结构,与翅片间存在较好的结合,因此,在无外部冲击(如人为触碰)的情况下,表面纳米结构不会受到大规模破坏。超疏水换热器在自身的结霜/化霜过程中,对表面纳米结构的破坏较少,因此,在超疏水换热器的安装、维修以及拆卸过程中,减少对翅片表面的触碰,可以很好地保护翅片表面的纳米结构。
其次,结霜/化霜过程对HTMS表面改性疏水材料与纳米结构的粘附性具有一定影响。为此,对超疏水换热器涂层的耐久性及使用寿命进行简单估算。假设电动汽车每天行驶60km,平均车速为20km/h,汽车每天运行时间约为3h,如图9a中,未结霜时原始压降为31.8Pa(第500s处),2690s后压降为62Pa,当换热器结霜后压降提高2.5倍时为最佳除霜时刻[20],按照正比例函数拟合,预测所需要的时间,则通过超疏水换热器的压降由未结霜时31.8Pa提高至111.3Pa时进行除霜,通过拟合,所需时间为5765s,超疏水换热器的化霜频率为每1.6h化霜一次,每天化霜约2次。电动汽车在冬季低温环境下运行时,需要进行热泵换热器的除霜化霜,以冬季时间较长的中国东北地区为例,假设一年中有6个月的寒冷季节需要进行化霜工作,则一年所需化霜次数为360次。前期研究结果表明,利用HTMS表面改性方法制备的疏水表面在结霜/化霜过程中,具有良好的耐久性,结霜/化霜过程对表面的疏水性能影响较小,在1000次结霜/化霜循环后表面疏水性能(接触角)未产生明显变化[21]。
因此,通过类比分析,预估通过HTMS疏水材料进行改性的超疏水换热器的使用寿命在2年以上。
03
针对纯电动汽车热泵型空调冬季制热循环中易出现的车外换热器结霜导致换热效率降低及除霜能耗问题,本文对换热器进行表面微纳结构制备及低表面能处理,成功制备了一种超疏水换热器,并试验研究了其延缓结霜机理及性能。在低温条件下,冷凝液滴在超疏水换热器表面能够自发合并导致液滴自弹跳现象,有效抑制冷凝液滴的粘附,进而延缓换热器表面结霜。通过超疏水处理可以有效减少换热器的含水率,在化霜条件下可以快速排出融霜,保持换热器翅片的高效换热性能。利用水热法和HTMS表面改性方法制备的疏水表面在结霜/化霜过程中,具有良好的耐久性,预估超疏水换热器的使用寿命约为2年以上。本文的主要结论如下:
a.在微观尺度下表征超疏水表面冷凝液滴的合并自弹跳现象,是延缓结霜的重要原因。
b.通过水热法和HTMS化学气相沉积方法实现超疏水换热器的制备,制热模式下换热器的风洞压降试验结果表明,相比于未经处理的换热器,超疏水换热器结霜时间延长70%以上,可以有效抑制电动汽车换热器结霜。
c.与未经处理换热器对比,超疏水换热器单位时间内所需化霜次数减少约40%以上。
d.通过含水率测试,超疏水换热器的含水率始终低于未经处理换热器的含水率,约为9.4%,可以保持换热器翅片的高效换热性能。
【参考文献】
[1] 胡志林, 张昶, 杨钫, 等. 电动汽车热泵空调系统技术研究[J]. 汽车文摘, 2019(5): 6-11.HU Z L, ZHANG C, YANG F, et al. Research on Heat PumpAir Conditioning System for Electric Vehicle[J]. AutomotiveDigest, 2019(5): 6-11.
[2] 李海军. 纯电动汽车用低温热泵型空调系统性能研究[D].西安: 西安建筑科技大学, 2015.LI H J. Study on Performance of Low Temperature HeatPump Air- Conditioning System for Pure Electric Vehicle[D].Xi’an:Xi’anUniversityofArchitectureandTechnology, 2015.
[3] 彭庆丰, 赵韩, 陈祥吉, 等. 电动汽车新型热泵空调系统的设计与试验研究[J]. 汽车工程, 2015, 37(12): 1467-1470.PENG Q F, ZHAO H, CHEN X J, et al. Design andExperimental Study of Novel Heat Pump Air ConditioningSystem for Electric Vehicles[J]. Automotive Engineering,2015, 37(12): 1467-1470.
[4] LORENTZEN G, PETTERSEN J. A New, Efficient andEnvironmentally Benign System for Car Air-Conditioning[J].International Journal of Refrigeration, 1993, 16(1): 4-12.
[5] LIU C C, ZHANG Y, GAO T Y, et al. PerformanceEvaluation of Propane Heat Pump System for ElectricVehicle in Cold Climate [J]. International Journal ofRefrigeration, 2018, 95: 51-60.
[6] GANESAN P, VANAKI S M, THOO K, et al. Air-Side HeatTransferCharacteristicsofHydrophobicandSuper-Hydrophobic Fin Surfaces in Heat Exchangers: A Review[J].International Communications in Heat and Mass Transfer,2016, 74: 27-35.
[7] XIA Y, ZHONG Y, HRNJAK P S, et al. Frost, Defrost, andRefrost and Its Impact on the Air-Side Thermal-HydraulicPerformance of Louvered-Fin, Flat-Tube Heat Exchangers[J]. International Journal of Refrigeration, 2006, 29(7): 1066-1079.
[8] ZHU J H, SUN Y Y, WANG W, et al. A Novel Temperature-Humidity- Time Defrosting Control Method Based on aFrosting Map for Air- Source Heat Pumps[J]. InternationalJournal of Refrigeration, 2015, 54: 45-54.
[9] 张毅, 张冠敏, 张莉莉, 等. 空气源热泵结霜机理及除霜/抑霜技术研究进展[J]. 制冷学报, 2018, 39(5): 13-24.ZHANG Y, ZHANG G M, ZHANG L L, et al. ResearchProgress on Frost Formation Mechanism of Air-Source HeatPumpandItsDefrosting/Anti- FrostingTechnology[J].Journal of Refrigeration, 2018, 39(5): 13-24.
[10] BOYINAKS,MAHVIAJ,CHAVANS,etal.Condensation Frosting on Meter- Scale Superhydrophobicand Superhydrophilic Heat Exchangers[J]. InternationalJournal of Heat and Mass Transfer, 2019, 145.
[11] MAHVI A J, BOYINA K, MUSSER A, et al. Superhy⁃drophobic Heat Exchangers Delay Frost Formation andEnhance Efficency of Electric Vehicle Heat Pumps[J].International Journal of Heat and Mass Transfer, 2021, 172.
[12] JHEE S, LEE K-S, KIM W-S. Effect of Surface Treatmentson the Frosting/Defrosting Behavior of a Fin- Tube HeatExchanger[J]. International Journal of Refrigeration, 2002,25(8): 1047-1053.
[13] KIM K, LEE K-S. Frosting and Defrosting Characteristicsof Surface-Treated Louvered-Fin Heat Exchangers: Effectsof Fin Pitch and Experimental Conditions[J]. InternationalJournal of Heat and Mass Transfer, 2013, 60: 505-511.
[14] LI L N, LIN Y K, RABBI K F, et al. FabricationOptimization of Ultra-Scalable Nanostructured Aluminum-Alloy Surfaces[J]. ACS Applied Materials & Interfaces,2021, 13(36): 43489-43504.
[15] YAN X, ZHANG L C, SETT S, et al. Droplet Jumping:Effects of Droplet Size, Surface Structure, Pinning, andLiquid Properties[J]. ACS Nano, 2019, 13(2): 1309-1323.
[16] LIU X L, CHEN H W, ZHAO Z H, et al. Self- JumpingMechanism of Melting Frost on Superhydrophobic Surfaces[J]. Scientific Reports, 2017, 7(1).
[17] 陈小娇, 武卫东, 汪德龙. 超疏水表面抑制结霜研究进展[J]. 表面技术, 2015, 44(2): 87-92.CHEN X J, WU W D, WANG D L. Rsearch Progress inAnti-Frosting Performance of Super-Hydrophobic Surfaces[J]. Surface Technology, 2015, 44(2): 87-92.
[18] 汪峰, 梁彩华, 张小松. 超疏水翅片表面的抑霜机理和融霜特性[J]. 工程热物理学报, 2016, 37(5): 1066-1070.WANG F, LIANG C H, ZHANG X S. Anti- FrostingMechanism and Frost Melting on Superhydrophobic FinSurface[J]. Journal of Engineering Thermophysics, 2016, 37(5): 1066-1070.
[19] 赵玲倩, 刘中良, 李丽艳, 等. 疏水性对竖直冷表面上自然对流结霜特性的影响[J]. 制冷学报, 2019, 40(3): 43-51.ZHAO L Q, LIU Z L, LI L Y, et al. Effect ofHydrophobicity on Frost Deposition on Vertical ColdSurfaces under Natural Convection Conditions[J]. Journalof Refrigeration, 2019, 40(3): 43-51.
[20] 张哲, 厉彦忠, 田津津, 等. 风冷热泵除霜的实验研究[J].低温与超导, 2003, 31(1): 36-38.ZHANG Z, LI Y Z, TIAN J J, et al. Experimental Study onthe Defrost of Air- Cooled Heat Pump[J]. Cryogenics andSuperconductivity, 2003, 31(1): 36-38.
[21] HOQUE M J, YAN X, QIU H Y, et al. Durability andDegradation Mechanisms of Antifrosting Surfaces[J]. ACSApplied Materials & Interfaces, 2023, 15(10): 13711-13723.

随着电子产品防水需求的不断提高,从原先的 IP54到现在的IP67IP68等级!市场上出现了防水透气膜和防水透音膜,目前这两种不同的材料应用被搞混了,今天便与大家一起讨论防水透气
最近各地降雨量激增,所以手机就难免会沾点水,作为生活中不可或缺的电子产品,防水已经成为一个十分重要重要功能,而且个人对目前的IP68手机市场是相当不满意的。为什么?太贵
自然界中荷叶具有出淤泥而不染的典型不沾水特性(学术上称为Cassie-Baxter状态),具有自清洁、抗结冰、减阻、抗腐蚀等广泛应用价值,而玫瑰花瓣则具有水滴高粘附特性(称为Wenze
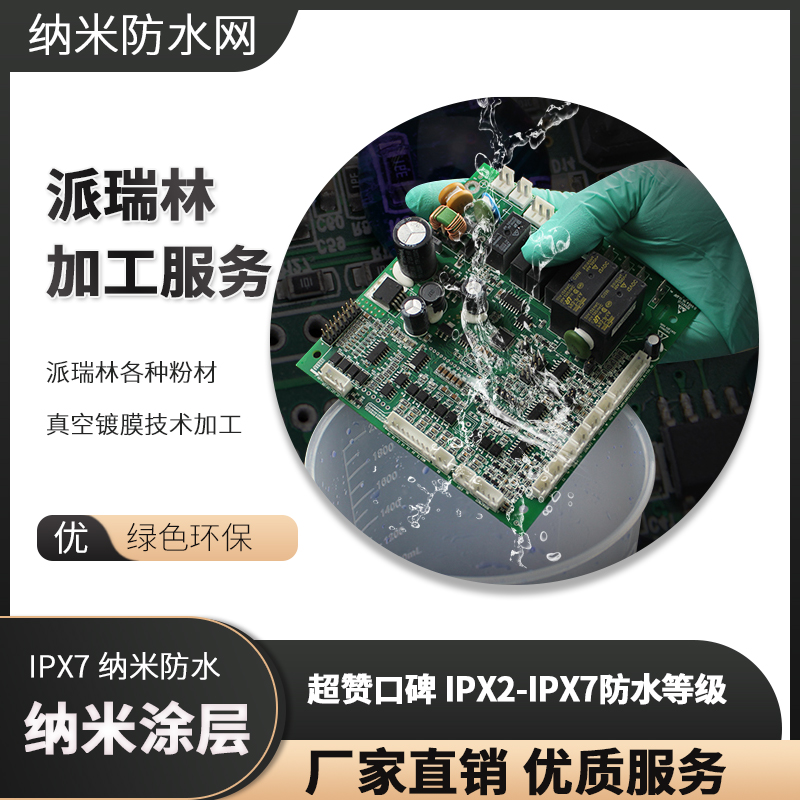
派瑞林各种粉材真空镀膜技术加工 纳米涂层防水处理
派瑞林各种粉材真空镀膜技术加工 纳米涂层防水处理
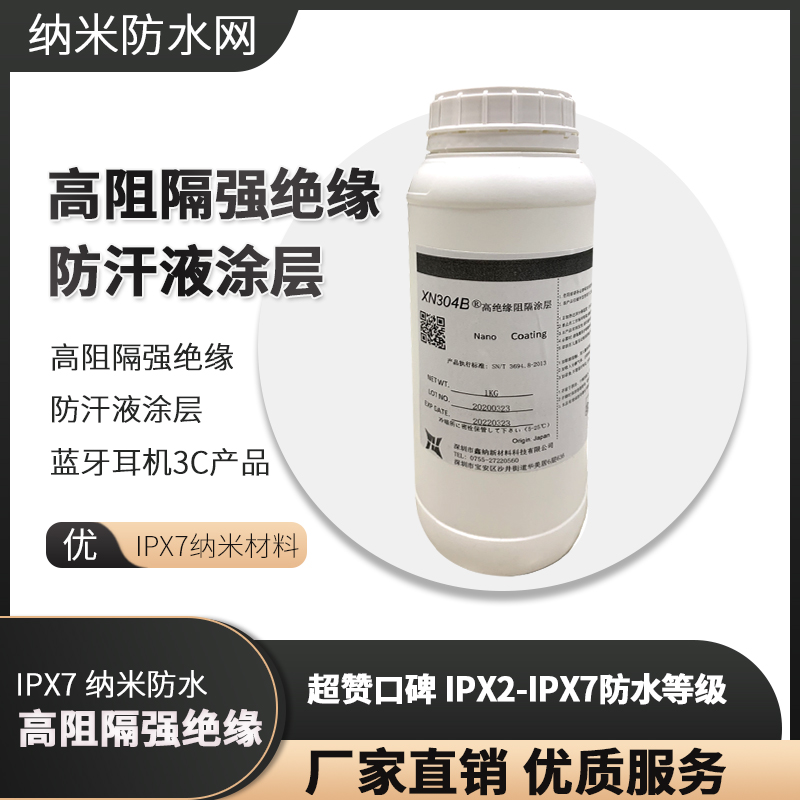
高阻隔强绝缘防汗液涂层蓝牙耳机3C电子产品IPX7纳米材料
高阻隔强绝缘防汗液涂层蓝牙耳机3C电子产品IPX7纳米材料
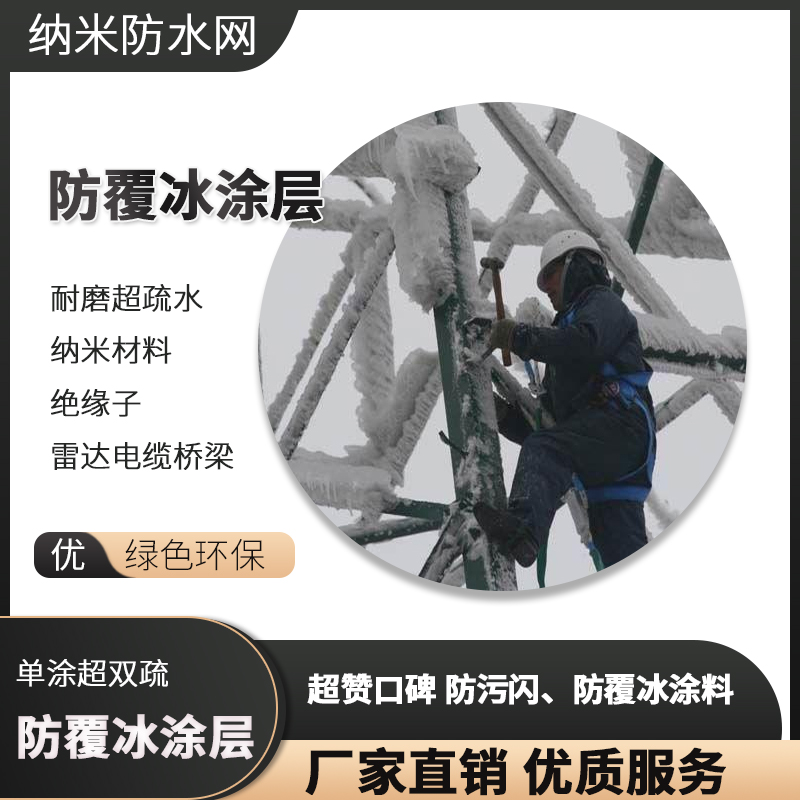
耐磨超疏水纳米材料 绝缘子架空导线电缆桥梁防覆冰涂层
耐磨超疏水纳米材料 绝缘子架空导线电缆桥梁防覆冰涂层
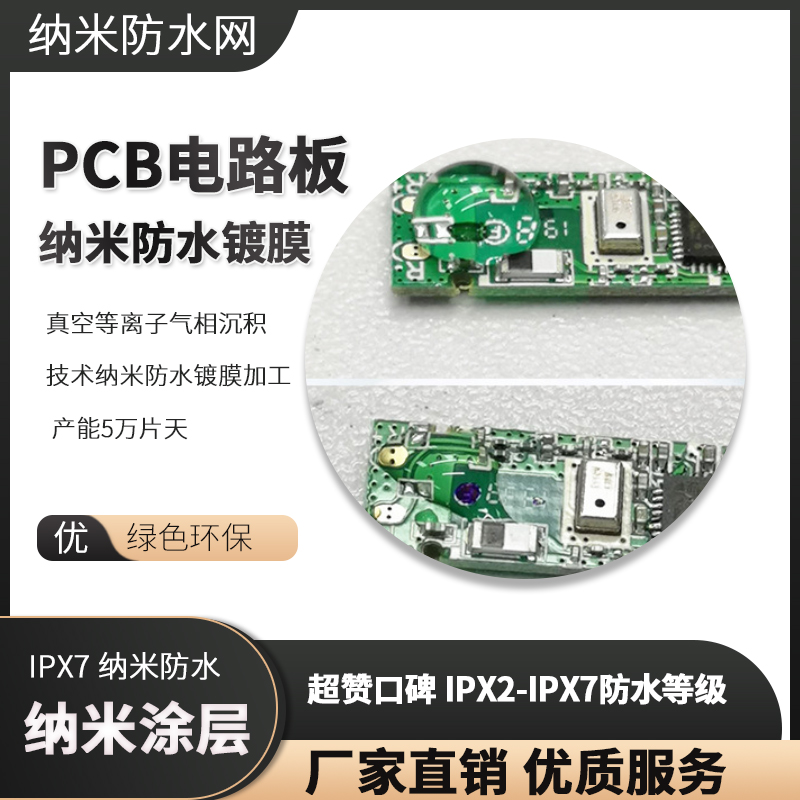
真空等离子气相沉积技术纳米防水镀膜加工 产能5万片天
真空等离子气相沉积技术纳米防水镀膜加工 产能5万片天
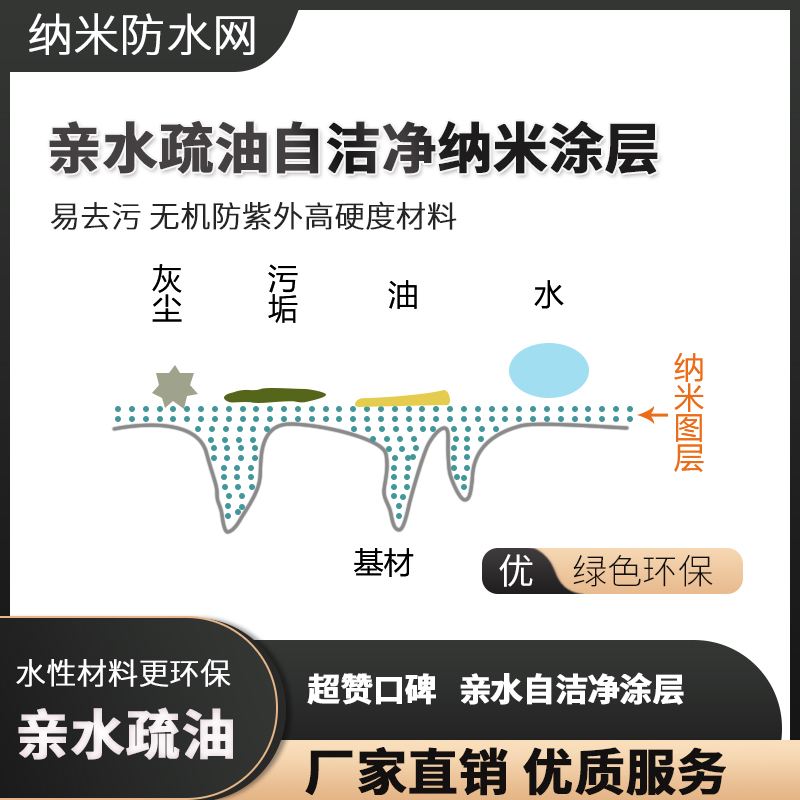
亲水疏油自洁净纳米涂层 易去污 无机防紫外高硬度材料
亲水疏油自洁净纳米涂层 易去污 无机防紫外高硬度材料
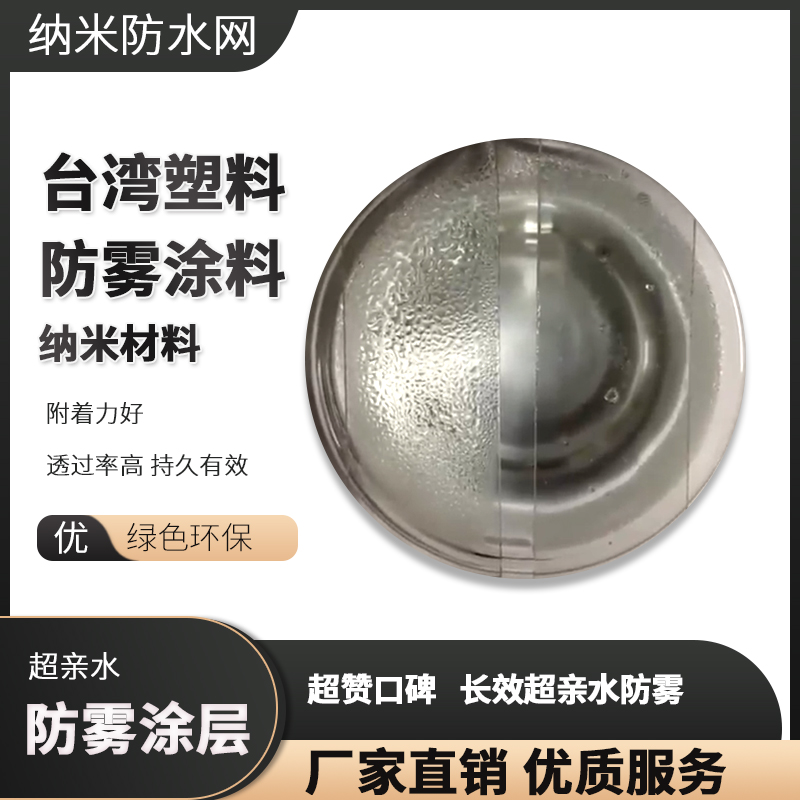
台湾超亲水防雾塑料专用 附着力好 透过率高 持久有效
台湾超亲水防雾塑料专用 附着力好 透过率高 持久有效